Solderable Polyurethane Enameled Aluminum Wire: A Comprehensive Overview
Solderable polyurethane enameled aluminum wire is a vital component in modern electrical engineering, offering exceptional performance across a wide variety of applications. This article provides an in-depth exploration of its properties, applications, and advantages, emphasizing its significance in producing high-quality electrical products. With impressive solderability, thermal class performance, and chemical resistance, this product has become a cornerstone in industries ranging from small motors to transformers.
What is Solderable Polyurethane Enameled Aluminum Wire?
Solderable polyurethane enameled aluminum wire is a specialized magnet wire coated with a layer of polyurethane enamel. This enamel not only provides superior insulation but also enables direct soldering, eliminating the need for prior coating removal. Known for its thermal resistance, winding performance, and chemical durability, it is widely used in coils, motors, and transformers.This type of wire is particularly valued for its thermal class 155 performance, which ensures consistent operation under high temperatures without compromising mechanical and electrical properties.
Key Features of Solderable Polyurethane Enameled Aluminum Wire
Feature | Description |
Direct Solderability | Eliminates the need for pre-stripping the enamel, simplifying the soldering process. |
Thermal Resistance | Operates efficiently in environments up to 155°C, meeting thermal class 155 standards. |
Chemical Resistance | Resistant to moisture, solvents, and other corrosive agents. |
High Winding Performance | Suitable for high-speed winding, ensuring precision and durability. |
Versatile Applications | Used in motors, transformers, relays, and voice coils. |
Product Outline
Below is a detailed breakdown of the product, organized into H3 subheadings to explain its properties, applications, and advantages.
1. What is Polyurethane Enamel?
Polyurethane enamel is a type of insulating varnish applied to magnet wires like aluminum and copper wires. Its primary role is to provide a reliable insulating layer that resists heat, moisture, and mechanical stress. Unlike other types of enamel, polyurethane enamel is specifically designed for direct soldering, making it a preferred choice for applications where fast assembly is critical.
2. Why Choose Aluminum Wire Over Copper Wire?
While copper wire has traditionally been the go-to material for magnet wire, aluminum wire offers distinct advantages:
- Lightweight: Aluminum is lighter, reducing the overall weight of electrical systems.
- Cost-Effective: It is more affordable than copper, making it ideal for budget-conscious applications.
- Solderability: When coated with polyurethane enamel, aluminum achieves excellent direct soldering properties.
3. How Does Polyurethane Enamel Improve Solderability?
The solderability of this wire lies in its polyurethane enamel coating, which melts effortlessly during the soldering process. This eliminates the need for time-consuming processes like removing the enamel coating manually. Additionally, it ensures:
- Stronger Connections: The enamel melts evenly, forming robust soldered joints.
- Simplified Production: Reduces production time in industries like motors and transformers.
4. Applications of Solderable Polyurethane Enameled Aluminum Wire
This wire finds applications in a wide range of industries due to its exceptional properties:
- Motors: Ensures reliable performance in high-temperature environments.
- Transformers: Provides efficient thermal and insulation properties.
- Voice Coils: Offers precise performance in audio applications.
- Relays and Solenoids: Ensures durability and resistance to wear.
5. Thermal Class 155 and Its Importance
The thermal class 155 rating signifies that this wire can withstand temperatures up to 155°C without degrading. This makes it suitable for applications demanding high levels of heat resistance, such as:
- Industrial Motors: Operates under continuous high-temperature conditions.
- High-Speed Winding Applications: Maintains performance even during rapid winding processes.
6. The Role of Insulation in Enameled Wire
Insulation is critical in preventing electrical short circuits and ensuring efficient energy transfer. The polyurethane insulation in these wires provides:
- High Dielectric Strength: Essential for preventing voltage leaks.
- Moisture Resistance: Protects the wire from environmental damage.
- Chemical Resistance: Ensures durability in harsh conditions.
7. Benefits of Using Solderable Polyurethane Enameled Aluminum Wire
This wire offers numerous advantages over traditional wires:
- Ease of Use: Direct soldering simplifies assembly processes.
- Durability: Resistant to abrasion and chemicals.
- Cost Savings: Aluminum is more cost-effective than copper.
8. What is the Recommended Wire Size Range?
The wire size ranges from 0.008 mm to 0.50 mm, accommodating a variety of applications. Smaller sizes are ideal for precision devices like voice coils, while larger sizes work well in motors and transformers.
9. How is the Wire Manufactured?
The manufacturing process involves several critical steps:
- Wire Drawing: Aluminum is stretched into precise diameters.
- Application of Polyurethane Enamel: The wire is coated with an even layer of insulating enamel.
- Curing Process: The enamel is cured to ensure durability and direct solderability.
10. Comparing Polyurethane Enamel to Polyester Enamel
While polyurethane enamel is prized for its direct soldering properties, polyester enamel offers better mechanical strength. For applications requiring direct solderability, polyurethane is the superior choice. However, for heavy-duty applications, polyester may be preferred.
Conclusion
Solderable polyurethane enameled aluminum wire is an essential product for industries demanding high-performance magnet wire solutions. Its direct solderability, thermal resistance, and chemical durability make it a top choice for applications ranging from motors to transformers. Whether you’re working with voice coils, relays, or high-speed winding, this wire delivers unmatched reliability and efficiency.By combining advanced manufacturing techniques with the unique properties of polyurethane enamel, this product offers a robust solution for modern electrical engineering challenges. Whether you’re prioritizing thermal class 155 performance, cost-efficiency, or ease of use, solderable polyurethane enameled aluminum wire exceeds expectations.
Why Choose Us
China’s Role in High-Tension Enameled Wire Manufacturing
As a global leader in enameled wire production, China provides high-quality high-tension winding wires tailored to international standards. Chinese manufacturers leverage advanced production techniques to ensure superior mechanical strength, insulation properties, and consistency in wire processing.
Key Manufacturing Strengths
State-of-the-Art Facilities: Equipped with precision metallurgy and automated insulation coating technologies.
Strict Quality Control: Compliance with JIS, IEC, and NEMA standards ensures high-performance output.
Competitive Pricing: Cost-effective solutions without compromising quality.
Customization Capabilities: Tailored wire specifications to meet diverse industry requirements.
Conclusion
High-tension enameled winding wires represent a crucial component in precision electrical applications. With advancements in tensile strength, conductivity, and insulation properties, these wires provide superior reliability and efficiency. As a leading global supplier, China continues to drive innovation and quality in high-tension enameled wire manufacturing, ensuring the highest industry standards for diverse technological applications.
Frequently Asked Questions
1. What is the primary advantage of high-tension enameled winding wire?
High-tension enameled winding wire offers significantly higher tensile strength compared to standard copper wire, reducing breakage risks in high-precision applications.
2. How does high-tension wire compare to pure copper wire in conductivity?
While high-tension wire has slightly lower conductivity than pure copper (ranging from 77% to 95%), it compensates with superior mechanical strength and durability.
3. What industries commonly use high-tension enameled wires?
These wires are widely used in electro-acoustic applications, telecommunications, mobile devices, and sensor technologies.
4. Why is China a leading manufacturer of high-tension enameled wire?
China’s advanced manufacturing capabilities, strict quality control, and cost-efficient production processes make it a top supplier in the global market.
5. Can high-tension enameled wire be customized for specific applications?
Yes, manufacturers offer tailored solutions with varying tensile strengths, insulation grades, and bonding methods to meet specific industrial requirements.
Why Choose Us
Enamelled Wires Factory Directly
As an established leader in the production of enamelled wires, we provide top-quality enamelled copper and aluminium wires from the largest and most advanced facility in China. Our patented system ensures seamless monitoring of production processes, guaranteeing the exceptional quality of our enamelled wires.
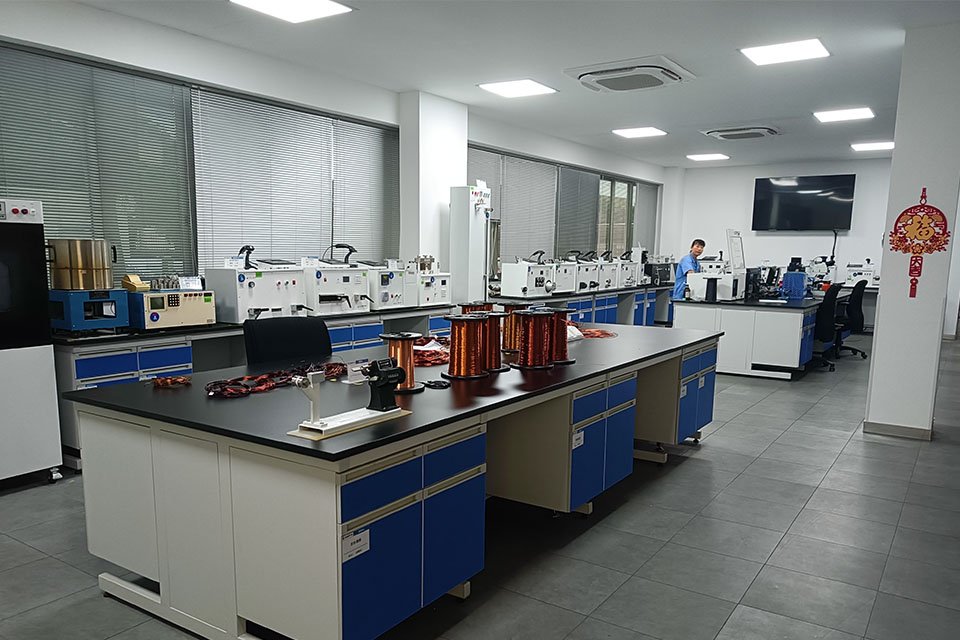
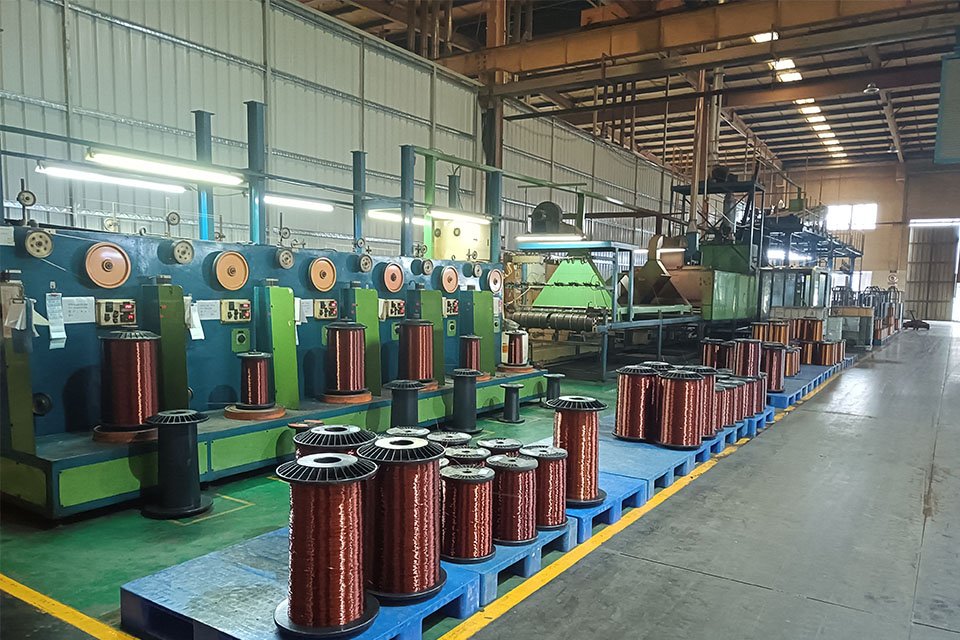
Many Years of Know-how as a Producer of Enamelled Wires
Leverage our extensive experience as a leading producer of enamelled wires. Operating from the largest and most advanced facility in China, we provide enamelled wires of superior quality. Our commitment to continuous investment in cutting-edge machinery and ongoing innovation in our research and development department ensures that we deliver products that enhance your processes and drive inspiration.
Individual Enamelled Wires Matching Your Requirements
As a producer of enamelled copper and aluminium wires, we tailor our products to meet your specific project needs. For suitable volumes, we offer customized enamelled wires from our extensive range. Our production process involves close collaboration between our sales team, application technology experts, and you, ensuring optimal results for your requirements.
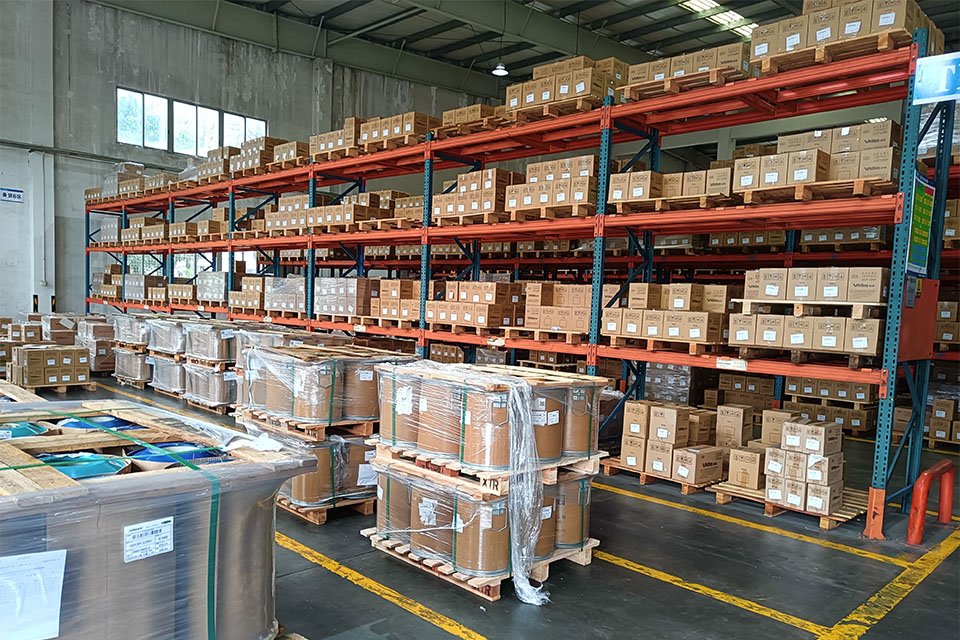
Frequently Asked Question
We have ISO9001,ISO14001,IATF16949 and UL certificates.
We are a factory.
We have a special QC department with 15 inspection personnel. Quality inspection team including incoming material, process and finished product inspection
Enamelled wires are available in insulation classes F-155, H-180, and C-200, which indicate their maximum operating temperatures in degrees Celsius
The temperature ratings typically range from 130°C to 220°C, depending on the insulation class and specific application requirements.
Enamelled aluminium wires are lighter and less expensive than copper wires but have slightly lower conductivity. Copper wires, on the other hand, offer higher conductivity and better mechanical strength but are heavier and more costly
Enamelled aluminium wires are ideal for use in large motors, transformers, and other applications where weight reduction is crucial without significantly compromising conductivity.
Enamelled copper wire is preferred in industries requiring high conductivity, such as in electronics, small motors, and applications where space is limited due to copper’s superior conductivity and strength.
Yes, we can customize enamelled wires to meet project-specific requirements, including different sizes, insulation types, and performance specifications.
Enamelled CCA Wire, Enamelled Aluminum Wire, Enamelled Copper Wire