Litz Wire: A Revolution in High-Frequency Electrical Conductivity
Litz wire is a specialized type of multi-stranded wire designed to reduce energy losses caused by the skin effect and proximity effect in high-frequency applications. Unlike standard conductors, litz wire is made up of multiple individually insulated strands twisted or braided in a specific pattern to improve efficiency. This unique construction allows it to handle alternating current (AC) more effectively than traditional solid or stranded wires.In this article, we’ll explore the various aspects of litz wire, including its construction, types, applications, and why it is the preferred choice for industries ranging from transformers to wireless power systems. Whether you’re a manufacturer, engineer, or industry expert, this guide will provide valuable insights into the benefits of using litz wire and how it can reduce AC losses in your designs.
What is Litz Wire?
Litz wire is short for “litzendraht,” a German term meaning “woven wire.” It is a conductor made up of many individually insulated strands that are twisted or braided in a specific pattern. This design minimizes energy losses caused by the skin effect and proximity effect, phenomena that occur in high-frequency AC circuits where current tends to flow on the surface of a conductor rather than evenly across its cross-section.
Key Features of Litz Wire
- Reduced AC Losses: The braided or twisted pattern ensures uniform current distribution, reducing energy losses.
- High-Frequency Efficiency: Perfectly suited for high-frequency power applications such as transformers, inductors, and wireless charging systems.
- Customization Options: Available in a variety of strand counts, sizes, and insulation materials to meet specific performance requirements.
How is Litz Wire Constructed?
The construction of litz wire involves twisting or braiding multiple individually insulated strands of magnet wire. These strands are arranged in a uniform pattern to ensure that each strand occupies every position in the cross-section of the wire equally over its length. This helps mitigate the uneven current distribution caused by the skin depth effect in high-frequency applications.
Materials Used
- Copper Wire: The primary conductor, offering excellent electrical conductivity.
- Insulation: Includes materials such as polyester, nylon, or enamel to protect individual strands and prevent short circuits.
- Outer Insulation: In some cases, the litz wire is further enclosed in an additional jacket for mechanical protection.
Types of Litz Wire
What Are the Key Litz Wire Types?
Litz wire comes in various types, each tailored to specific applications. These include:
- Unserved Litz Wire: Basic construction without additional outer protection.
- Served Litz Wire: Includes a protective layer of silk, nylon, or textile for enhanced durability and smoother winding.
- Custom Litz Wire: Fully customizable designs to meet unique requirements, such as specific strand counts, insulation materials, or thermal ratings.
Each type offers unique benefits depending on the application, from wire used in transformers to high-frequency litz wire in wireless power systems.
How Does Litz Wire Reduce AC Losses?
Understanding AC Losses in High-Frequency Applications
In high-frequency applications, AC losses occur due to the skin effect (current flowing on the surface of the conductor) and the proximity effect (interaction of magnetic fields between nearby conductors). These effects increase the resistance of the wire, reducing efficiency.
How Litz Wire Mitigates These Effects
- Skin Effect Reduction: By breaking the conductor into multiple individually insulated strands, litz wire ensures that current flows more evenly, reducing resistance.
- Proximity Effect Mitigation: The twisted or braided pattern minimizes magnetic field interactions, further reducing energy losses.
Using litz wire in high-frequency designs significantly improves efficiency and reduces heat generation.
Applications of Litz Wire
1. Transformers and Inductors
Litz wire is widely used in transformers and inductors, especially in high-frequency designs. Its ability to handle high AC currents while minimizing losses makes it ideal for use in these critical components.
Applications of Served Litz Wire
1. Transformers and Inductors
Litz wire is widely used in transformers and inductors, especially in high-frequency designs. Its ability to handle high AC currents while minimizing losses makes it ideal for use in these critical components.
2. Wireless Power Systems
In wireless charging applications, high-frequency litz wire ensures efficient energy transfer by minimizing resistance and heat buildup. This makes it a popular choice for wireless battery chargers and other similar technologies.
3. Switching Power Supplies
Litz wire is commonly found in switching power supplies, where it helps maintain high efficiency and reliability under varying load conditions.
What Are the Benefits of Using Litz Wire?
1. Improved Efficiency
The unique construction of litz wire ensures low resistance and minimal energy losses, even in high-frequency power applications.
2. Enhanced Durability
The addition of outer insulation or serving materials protects the wire from mechanical stress, ensuring long-lasting performance.
3. Customization Options
Manufacturers like We offer custom litz wire solutions, allowing you to tailor the wire’s design to your specific requirements, such as strand count, insulation material, and thermal performance.
Technical Specifications of Litz Wire
Feature | Specification |
Strand Diameter | 0.020mm to 0.60mm |
Number of Strands | 2 to 36,000 |
Insulation Materials | Polyester, Nylon, Enamel |
Thermal Class | 155°C, 180°C, 200°C, 220°C |
Cross-Section Area | Up to 50mm² |
Applications | Transformers, Inductors, Wireless Systems |
How to Choose the Right Litz Wire?
1. Consider the Operating Frequency
Select a litz wire design that matches the frequency of the current in your application. Higher frequencies require finer strands and more precise construction.
2. Evaluate Thermal Requirements
Choose a thermal class that can handle the heat generated in your application. Options range from 155°C to 220°C, depending on the insulation material.
3. Strand Count and Diameter
The number of strands and their diameter determine the wire’s current-carrying capacity. Applications requiring higher currents benefit from larger strand counts.
How is Litz Wire Manufactured?
The manufacturing process of litz wire involves:
- Stranding: Multiple individually insulated strands are twisted or braided together.
- Insulating: Each strand is coated with protective materials like polyester or enamel.
- Serving (Optional): An additional layer of silk, nylon, or textile may be applied for mechanical protection.
Manufacturers like our Wire Technologies ensure strict quality control during production, resulting in high-quality litz wire products.
Conclusion: Why Choose Litz Wire for Your Application?
Litz wire is the ultimate solution for reducing AC losses in high-frequency applications. Its unique construction and ability to mitigate the skin effect and proximity effect make it an essential component for transformers, inductors, wireless systems, and more.
Key Takeaways
- Reduced AC Losses: Litz wire minimizes resistance in high-frequency circuits.
- Customizable Design: Tailored to meet specific application needs.
- Wide Range of Applications: From transformers to wireless power systems.
If you’re looking for high-quality litz wire products, contact manufacturers like New England Wire Technologies to explore custom solutions tailored to your requirements. Request a quote today to improve the efficiency of your high-frequency designs!
Why Choose Us
China’s Role in High-Tension Enameled Wire Manufacturing
As a global leader in enameled wire production, China provides high-quality high-tension winding wires tailored to international standards. Chinese manufacturers leverage advanced production techniques to ensure superior mechanical strength, insulation properties, and consistency in wire processing.
Key Manufacturing Strengths
State-of-the-Art Facilities: Equipped with precision metallurgy and automated insulation coating technologies.
Strict Quality Control: Compliance with JIS, IEC, and NEMA standards ensures high-performance output.
Competitive Pricing: Cost-effective solutions without compromising quality.
Customization Capabilities: Tailored wire specifications to meet diverse industry requirements.
Conclusion
High-tension enameled winding wires represent a crucial component in precision electrical applications. With advancements in tensile strength, conductivity, and insulation properties, these wires provide superior reliability and efficiency. As a leading global supplier, China continues to drive innovation and quality in high-tension enameled wire manufacturing, ensuring the highest industry standards for diverse technological applications.
Frequently Asked Questions
1. What is the primary advantage of high-tension enameled winding wire?
High-tension enameled winding wire offers significantly higher tensile strength compared to standard copper wire, reducing breakage risks in high-precision applications.
2. How does high-tension wire compare to pure copper wire in conductivity?
While high-tension wire has slightly lower conductivity than pure copper (ranging from 77% to 95%), it compensates with superior mechanical strength and durability.
3. What industries commonly use high-tension enameled wires?
These wires are widely used in electro-acoustic applications, telecommunications, mobile devices, and sensor technologies.
4. Why is China a leading manufacturer of high-tension enameled wire?
China’s advanced manufacturing capabilities, strict quality control, and cost-efficient production processes make it a top supplier in the global market.
5. Can high-tension enameled wire be customized for specific applications?
Yes, manufacturers offer tailored solutions with varying tensile strengths, insulation grades, and bonding methods to meet specific industrial requirements.
Why Choose Us
Enamelled Wires Factory Directly
As an established leader in the production of enamelled wires, we provide top-quality enamelled copper and aluminium wires from the largest and most advanced facility in China. Our patented system ensures seamless monitoring of production processes, guaranteeing the exceptional quality of our enamelled wires.
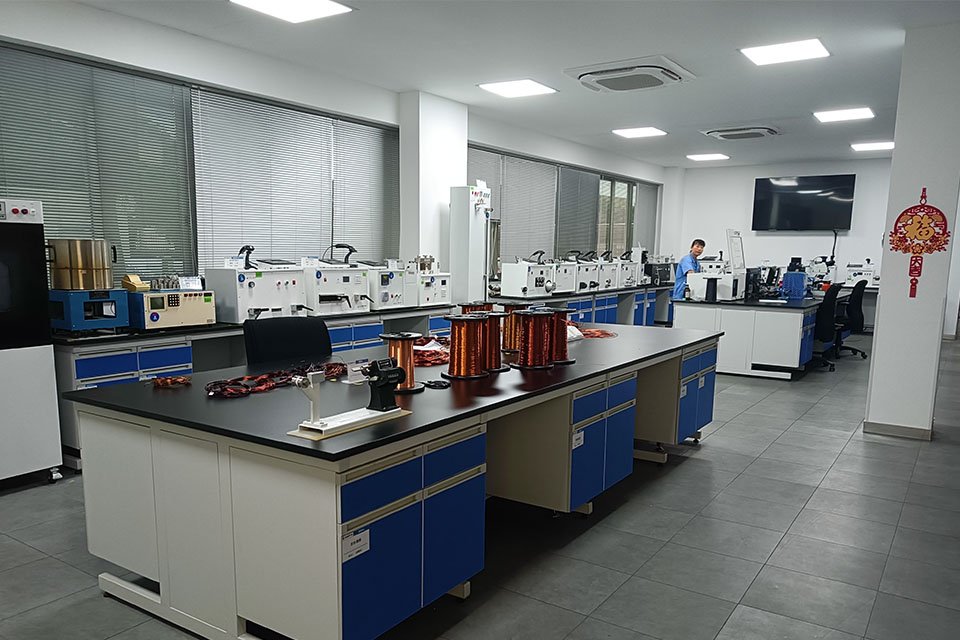
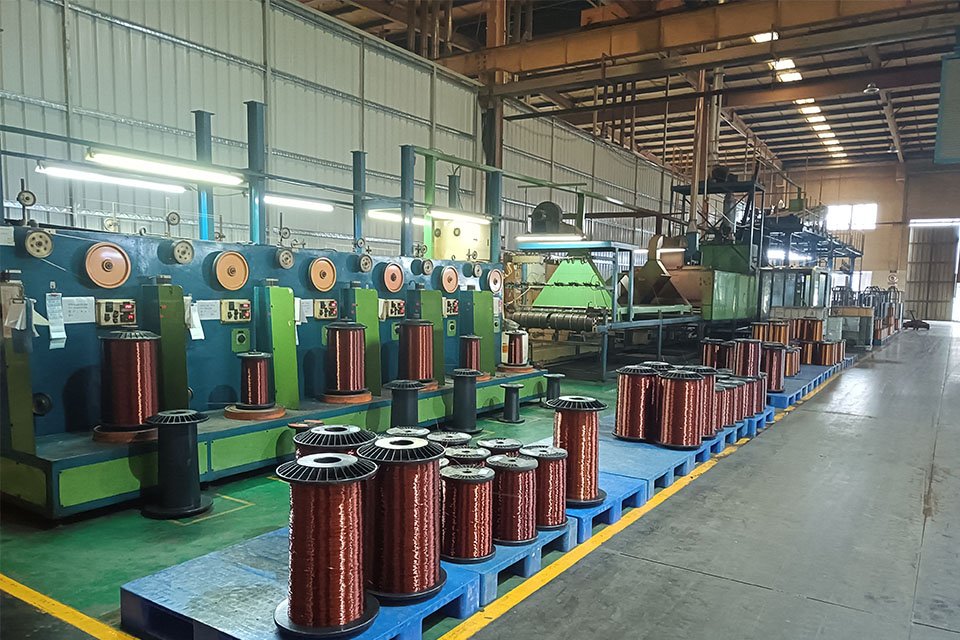
Many Years of Know-how as a Producer of Enamelled Wires
Leverage our extensive experience as a leading producer of enamelled wires. Operating from the largest and most advanced facility in China, we provide enamelled wires of superior quality. Our commitment to continuous investment in cutting-edge machinery and ongoing innovation in our research and development department ensures that we deliver products that enhance your processes and drive inspiration.
Individual Enamelled Wires Matching Your Requirements
As a producer of enamelled copper and aluminium wires, we tailor our products to meet your specific project needs. For suitable volumes, we offer customized enamelled wires from our extensive range. Our production process involves close collaboration between our sales team, application technology experts, and you, ensuring optimal results for your requirements.
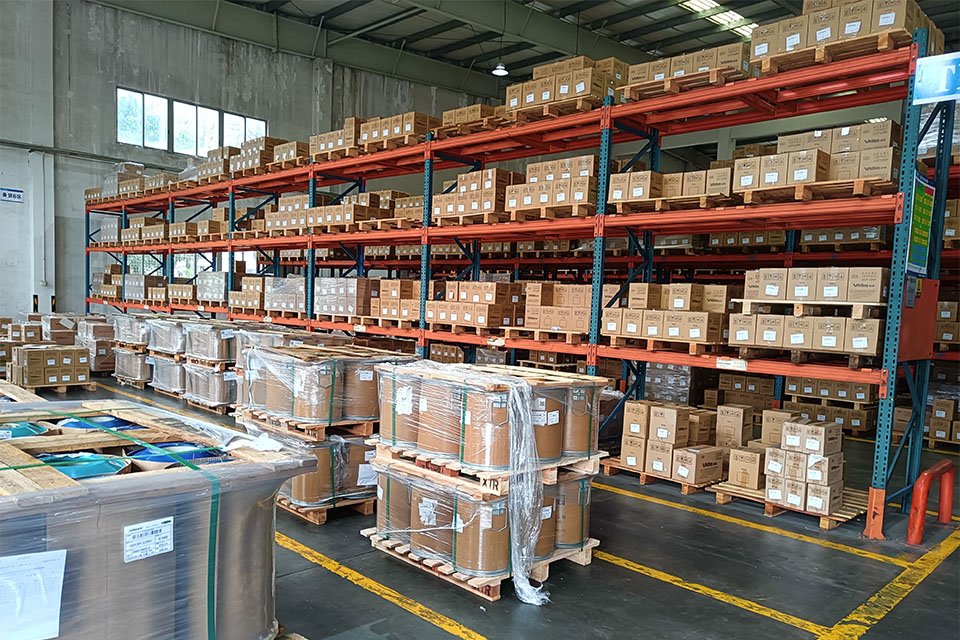
Frequently Asked Question
We have ISO9001,ISO14001,IATF16949 and UL certificates.
We are a factory.
We have a special QC department with 15 inspection personnel. Quality inspection team including incoming material, process and finished product inspection
Enamelled wires are available in insulation classes F-155, H-180, and C-200, which indicate their maximum operating temperatures in degrees Celsius
The temperature ratings typically range from 130°C to 220°C, depending on the insulation class and specific application requirements.
Enamelled aluminium wires are lighter and less expensive than copper wires but have slightly lower conductivity. Copper wires, on the other hand, offer higher conductivity and better mechanical strength but are heavier and more costly
Enamelled aluminium wires are ideal for use in large motors, transformers, and other applications where weight reduction is crucial without significantly compromising conductivity.
Enamelled copper wire is preferred in industries requiring high conductivity, such as in electronics, small motors, and applications where space is limited due to copper’s superior conductivity and strength.
Yes, we can customize enamelled wires to meet project-specific requirements, including different sizes, insulation types, and performance specifications.
Enamelled CCA Wire, Enamelled Aluminum Wire, Enamelled Copper Wire